Shake 'em and bake 'em... literally.
Moving on into the labs, the next area is where QNAPs gear is tested for heat and humidity tolerances. ICP has an array of ovens that raise or lower the ambient temperature way above or below what would be considered ‘normal’ limits of operation, to see how the products perform.These ovens can also control the humidity and, combined with the temperature, the dew point. This is actually pretty important as the temperature and percentage humidity (as well as pressure) affects at what point water will condense out of the atmosphere and onto the product under testing.
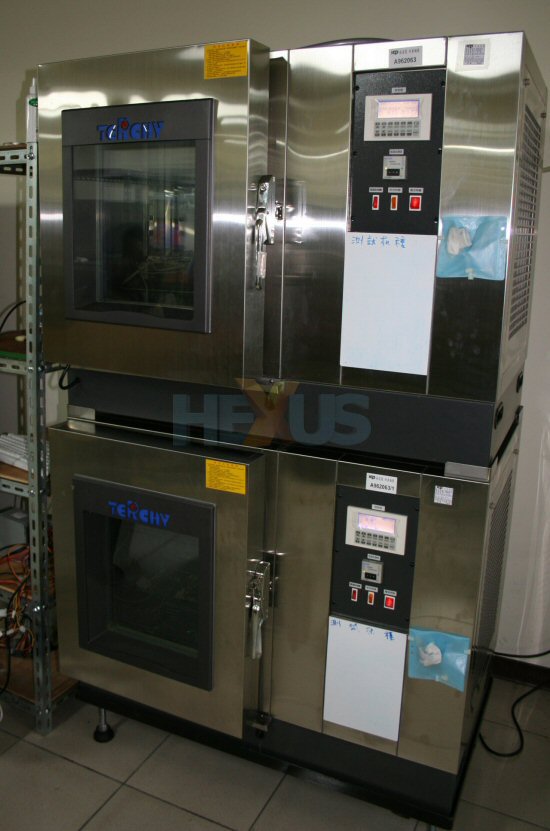
At lower temperatures you need less water vapour in the air for condensation to start. Similarly, higher temperatures require a higher humidity percentage before moisture drops out onto the board. Now, as you can see in the image below, this QNAP board is running, wired up to kit outside of the oven. This is so the tests are based purely on the board and not other factors such as the drives fitted etc.
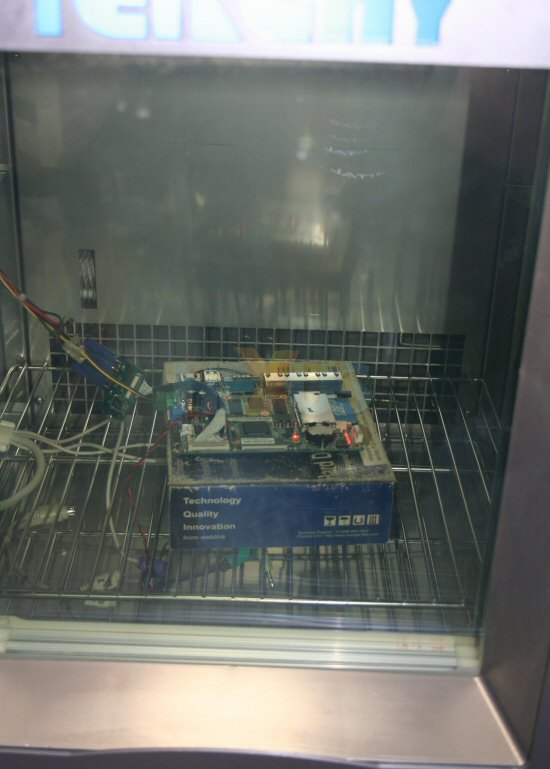
A secondary feature of these tests is to see how the boards perform doing the same jobs at different temperatures and humidity levels and this poor board here is rebuilding a RAID array for something like the tenth time. Also, it gives QNAP a chance to check the build quality of their boards as temperature fluctuations stress out components as well as soldered connections through expansion and contraction.
There’s more to come on the testing of the actually products, but let’s just briefly divert over to this interesting looking machine, which, a bit like that Dyson advert, drop tests the packaged product. It’s basically a mechanical trapdoor which tests box integrity for a range of shapes and weights, dropping them from a variety of heights according to the ISTA (International Safe Transit Assocation) specs.
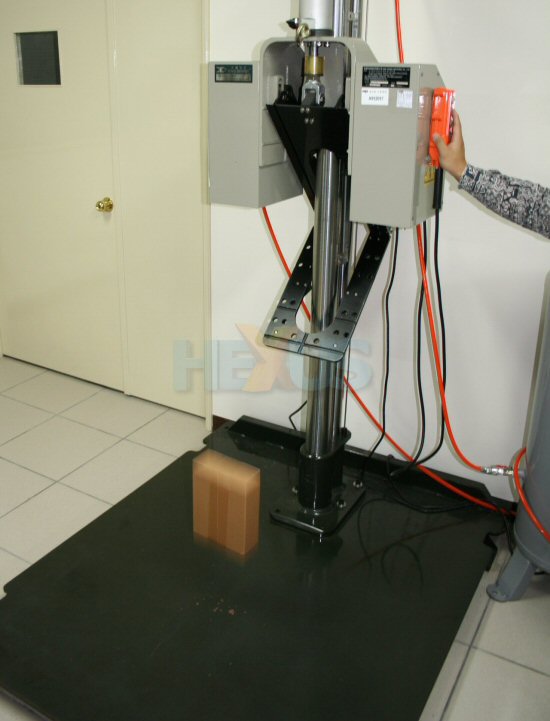
Did you know that each box has to survive a total of thirteen drops? 4 onto a corner, 3 on the edges and 6 on the sides… that’ll pretty much simulate some courier deliveries (if you combined it with the soak testing I guess…) Boxes up to 21lb in weight have to be dropped from 38 inches whilst a huge 150lb or more box only has to take a 6 inch drop… not that I could lift 150lbs so I guess that’s about right. Oddly enough there wasn’t a ‘being rattled about in the back of a van being driven by surly driver with no consideration for the damage he is doing’ test… but there was something similar.
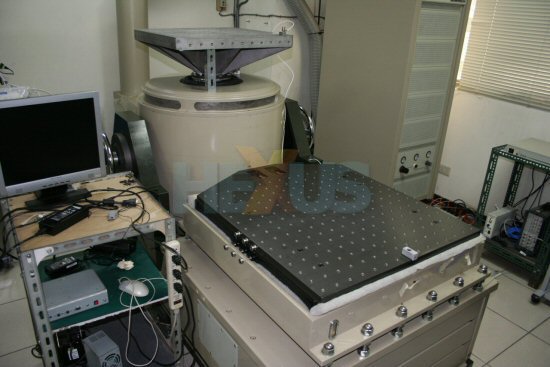
This beast of a machine tests vibration in all three axis, vertical, longitudinal and lateral and can even test vibration on an incline by tilting up to 90⁰ from horizontal. And to make sure the test replicates rattling around in the back of a van as closely as possible, it has two vibration settings, one is a standard back and forth and the other is a more stressful random motion which subjects the contents to higher forces as the direction changes more violently. Apparently a washing machine on full spin with an offset load has nothing on this thing when it’s running.