Self certification ability
Mike Lin's team manage the safety and certification labs at FSP's offices in Taoyuan. It accepts PSU designs from any of FSP's R&D labs from all over the world and is certified by UL, a company we touched on in our PSU roundup. Underwriters Laboratories are one of the cert houses that test almost anything to make sure it's fit for purpose. That testing is hugely extensive and expensive, which is why FSP have invested heavily in a lab that's able to do what UL does, certified by UL themselves, allowing FSP to save time and money on cert testing for their products.
While the lab can't provide self approval for all the safety and compliance marks for all the markets they address, data produced by the lab can assist to get the extra certification and compliance a product needs.
Mike explained that for most designs produced at the C2 phase it's usually 2 weeks for testing and 2 weeks for verification, to make sure the design can proceed to C8 and mass production.
Mike also explains that safety is a consideration starting at C1. His team makes sure the engineers responsible for the initial layout and component choice are sticking to the basics in terms of safety considerations, so the design isn't flawed from a safety perspective in any glaring way.
So when his guys and gals get a design for testing and verification, they test everything from compliance with the Low Voltage Directive, how the PSU performs in terms of electromagnetics (EMI and EMT), to how hot it gets to make sure thermal performance is more than adequate for where the PSU will be installed.
The LVD testing includes making sure touch current won't kill you should any part of the PSU short. They actively induce a failed component to create a short, then monitor current to make sure that if you're exposed to it, it won't end badly. Electricity can kill, obviously, so Mike's lab is there to make sure a PSU failure is only catastrophic internally. More on that soon.
It's a time consuming process, especially when the lab is performing overload testing. It takes 2 to 3 hours per stepped test, per output, to verify overload performance. On a supply with 6 outputs say, that's a large chunk of the 4 weeks it usually takes to verify and pass the labs testing.
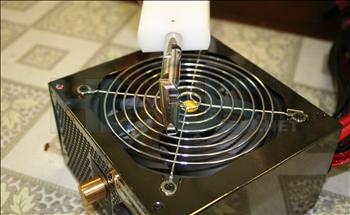
See that? It's a mechanical finger, precisely machined to a set spec that simulates an average human finger, which can be connected to monitoring hardware to evaluate whether that finger can touch anything dangerous. Costing the high side of £5000, that finger and many others are available to Mike's team for touch testing all manner of PSU, simulating the poking of screwdrivers where they should be and much more.